La capacité à optimiser les processus de fabrication et de maintenance des produits fait généralement toute la différence entre des opérations fluides et des interruptions de service dans le secteur industriel. Réduire les délais et anticiper les besoins constituent ainsi des priorités pour améliorer la productivité tout en limitant les coûts. Quelles sont donc les méthodes les plus efficaces pour y parvenir ? On vous explique tout !
Intégrez un outil de gestion du cycle de vie des produits (PLM)
Cette solution numérique vous offre une vision globale et centralisée, car elle rassemble l’intégralité des informations liées à un produit, de la phase initiale de conception jusqu’à son retrait. L’outil permet de limiter les silos entre les départements en rendant les données facilement accessibles aux différents services impliqués. Vous pouvez également vous servir d’un logiciel de gestion du cycle de vie des produits pour assurer une meilleure coordination entre les équipes et stimuler la communication.
Grâce au PLM, le suivi des modifications est par ailleurs facilité, ce qui diminue radicalement les risques de duplications ou d’erreurs coûteuses. Dès qu’une adaptation ou une mise à jour est apportée, elle devient immédiatement disponible pour toutes les parties prenantes, ce qui élimine les délais qui freinent l’avancement du développement.
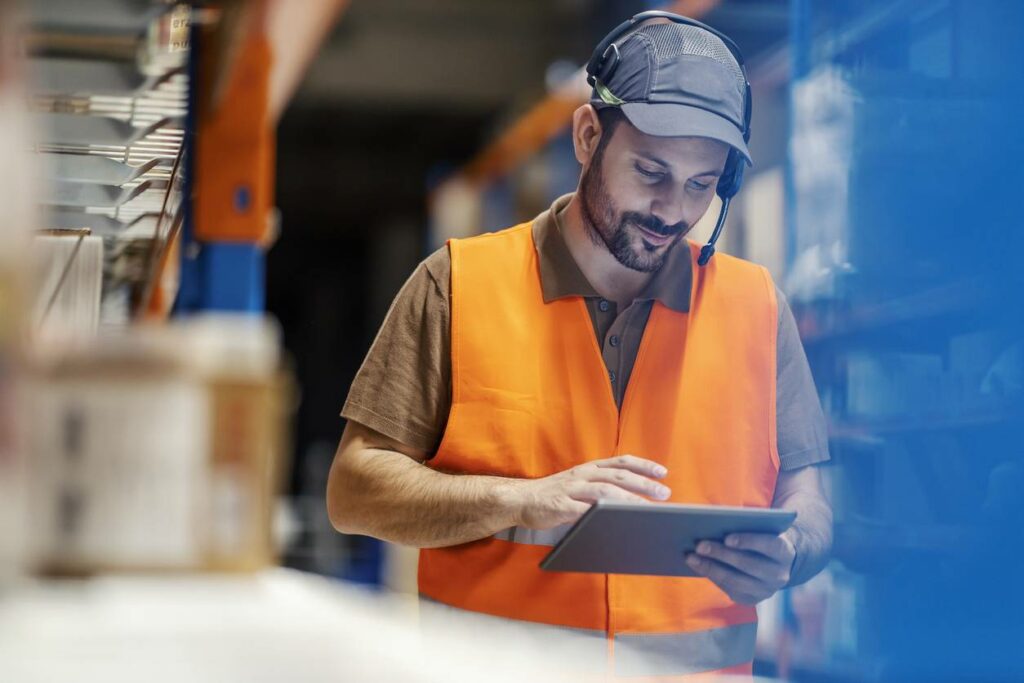
Utilisez la maintenance prédictive
Lorsque vous utilisez des capteurs intelligents, vous pouvez évaluer l’état de chaque équipement et détecter les signes avant-coureurs de dysfonctionnement bien avant qu’ils ne deviennent problématiques. Ces dispositifs sophistiqués mesurent divers paramètres, tels que la température, les vibrations ou la consommation d’énergie, et transmettent les informations pour une analyse continue. Avec cette approche, vous anticipez les besoins d’intervention, ce qui maintient le rythme de production sans contrainte.
L’intégration de solutions IoT permet quant à elle une surveillance accrue de vos installations et offre une vue constante sur l’état des machines. Chaque fluctuation anormale ou déviation par rapport aux standards de performance est aussitôt signalée, ce qui vous donne la possibilité d’intervenir de manière proactive et ciblée. En suivant cette méthode, vous optimisez l’utilisation des ressources et limitez les répercussions des pannes.
La maintenance prédictive génère également des économies substantielles, puisqu’elle réduit les frais associés aux réparations d’urgence. Grâce à cette stratégie, vous agissez avant que le matériel ne se dégrade, ce qui prolonge la durée de vie des actifs et minimise les dépenses liées aux remplacements imprévus. Cette réduction des coûts se traduit directement par une amélioration de la rentabilité et de la compétitivité.
Mettez en place une gestion des stocks en temps réel
Avec cette approche, vous pourrez anticiper et avoir un contrôle précis sur les besoins. Cela favorise une continuité fluide dans la chaîne de production et limite les risques de ralentissement dus à des manques ou à des excédents. L’utilisation de logiciels connectés pour gérer l’inventaire vous assure par ailleurs une visibilité constante sur l’ensemble des ressources. Ces outils permettent d’ajuster les niveaux en fonction de la demande, en alignant instantanément l’approvisionnement aux prévisions. Par ce biais, vous réduisez les stocks inactifs pour améliorer le flux des opérations et diminuer les immobilisations coûteuses.
De plus, les systèmes numériques modernisent vos méthodes et apportent une réponse rapide aux variations de consommation, ce qui garantit une flexibilité accrue face aux fluctuations du marché. La bonne gestion des quantités disponibles entraîne également une diminution des frais liés au stockage. Lorsque vous limitez les surfaces nécessaires et que vous évitez les accumulations inutiles, vous optimisez vos espaces et concentrez les ressources sur les besoins immédiats de production.
Commentaires récents