La qualité d’un assemblage dépend du choix des éléments de fixation. Parmi eux, le rivet assure une liaison robuste entre deux pièces, même quand l’accès est limité à une seule face. Facile à poser et résistant dans le temps, il s’emploie dans de nombreux domaines comme l’aéronautique, l’industrie automobile et le bâtiment. Tous les modèles n’offrent toutefois pas des performances égales. Avant de faire votre choix, vous devez ainsi examiner différents facteurs pour éviter les erreurs susceptibles de fragiliser la structure ou d’entraîner une défaillance prématurée. Comment contrôler la tenue mécanique ? Pourquoi prendre en compte l’environnement d’utilisation ? On vous explique tout !
Choisissez le matériau le plus adapté pour vos rivets
L’aluminium convient aux supports légers et qui ne sont pas soumis à des efforts considérables. Sa stabilité chimique, qui en fait un allié de choix pour les applications en milieu humide, est son avantage principal. L’acier garantit en revanche une robustesse supérieure. Disponible sous forme zinguée auprès de fournisseurs spécialisés, il assure une meilleure protection contre l’oxydation.
Comme on peut le voir avec Gfix par exemple, les rivets en acier inoxydable, notamment, se démarquent par leur durabilité accrue. Le cuivre, apprécié pour sa malléabilité, permet quant à lui un sertissage plus efficace et une bonne conductivité, un atout dans les secteurs électroniques et électriques. Enfin, le laiton représente une solution intéressante pour les installations qui requièrent une excellente tolérance aux vibrations.
Vérifiez la résistance mécanique requise
Chaque assemblage doit supporter des charges spécifiques sans compromettre sa solidité. Les rivets pleins se distinguent par leur forte capacité à absorber les efforts mécaniques. Cette caractéristique les rend adaptés aux structures soumises à des tensions élevées. Les modèles aveugles facilitent pour leur part la fixation quand l’accès à l’arrière des pièces est limité. Ils garantissent une bonne tenue sous des exigences modérées.
Pour ce qui est des versions à rupture de tige renforcée, elles augmentent la résistance aux forces d’arrachement et réduisent les risques de déformation. Tenez également compte de l’orientation et de l’intensité des sollicitations lors de votre choix. Une liaison confrontée à des tractions répétées requiert des attaches capables de conserver leur intégrité sans s’allonger. Pour des assemblages en cisaillement, privilégiez des éléments conçus pour bien répartir les charges.
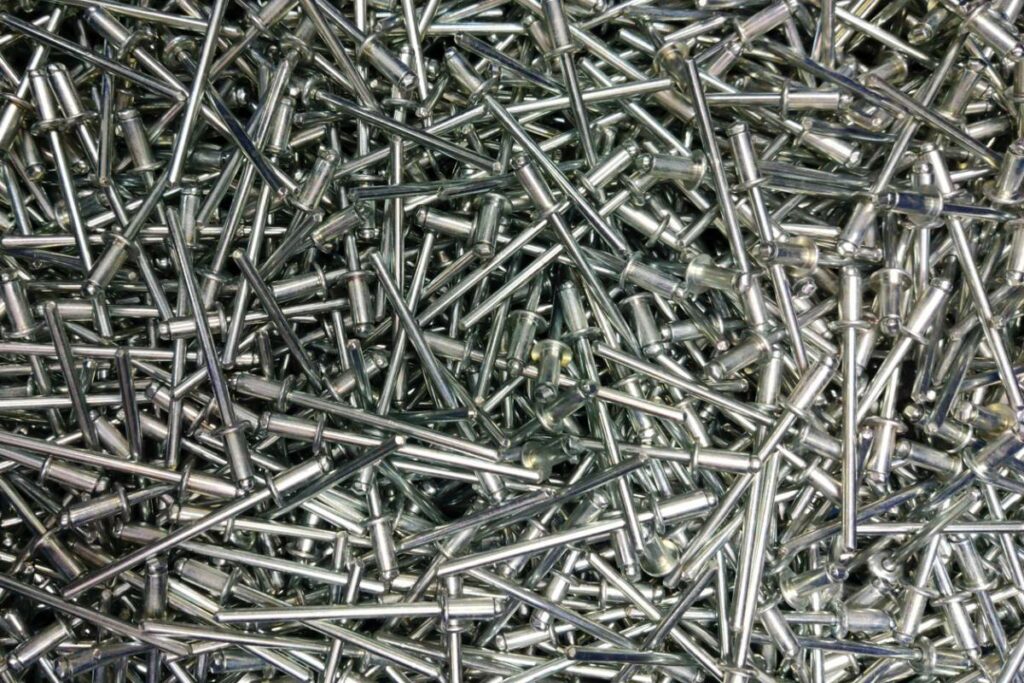
L’importance du bon diamètre pour une fixation optimale
Un dimensionnement précis assure un assemblage fiable et durable. Un rivet très fin compromet la solidité de l’ensemble, tandis qu’un composant trop large risque d’endommager les matériaux pendant le rivetage. Un diamètre qui correspond à l’épaisseur totale des pièces à fixer garantit en revanche une répartition homogène des efforts et empêche tout affaiblissement structurel.
Le perçage influe par ailleurs de manière directe sur la qualité du maintien. Un trou serré complique par exemple l’insertion et provoque parfois des déformations. Un trop grand espace est quant à lui susceptible de réduire l’efficacité du sertissage en générant des mouvements indésirables. Un ajustement optimal entre la tige de l’attache et le passage prévu permet une tenue stable et sans jeu. Il limite ainsi les vibrations et les risques d’usure prématurée.
Choix de rivets : tenez compte des conditions d’exposition
Un contact prolongé avec l’humidité, qui accélère l’oxydation de certains métaux, compromet la résistance au fil du temps. Le titane est alors une solution efficace pour éviter la corrosion dans des milieux exigeants comme l’aéronautique et l’industrie chimique. Ce matériau, qui combine une excellente résistance face aux agents agressifs et une grande légèreté, est idéal pour les applications soumises à des contraintes sévères. De plus, les températures extrêmes altèrent la stabilité des matières. Un rivet exposé à des variations thermiques considérables doit conserver sa structure sans se dilater ou se fragiliser. Dans ce cas, le laiton et le cuivre supportent mieux ces conditions. Les alliages à base de nickel résistent également à la chaleur sans perdre leurs propriétés mécaniques.
Commentaires récents