Composant essentiel de nombreuses machines de produits et d’usinages, les centrales hydrauliques industrielles ont un rôle central dans la capacité de production de nombreuses entreprises. Leur maintenance régulière voire leur dépannage rapide sont par conséquent cruciaux pour garantir leur bon fonctionnement et éviter d’éventuelles pannes coûteuses. Comprendre les mécanismes de ces centres d’énergie est essentiel pour maximiser leur rendement et prolonger leur durée de vie.
Comprendre l’importance des centrales hydrauliques industrielles
Comme l’indique le nom de ces machines, les centrales hydrauliques industrielles ont pour fonction de transformer l’énergie hydraulique en énergie mécanique. Elles alimentent diverses machines et équipements industriels dans des secteurs tels que l’industrie l’automobile, mais aussi l’agriculture ou la construction.
Ces systèmes complexes sont composés de plusieurs éléments clés tels que pompes, vérins, moteurs et réservoirs. Chacun de ces composants doit fonctionner parfaitement pour garantir une production continue et efficace. Une centrale hydraulique fonctionne en extrayant de l’énergie d’un fluide hydraulique comprimé, puis en convertissant cette énergie en force mécanique. Ce mécanisme repose sur le passage du fluide à travers différents composants avant d’atteindre les actuateurs, tels que les vérins et les moteurs.
Les pompes hydrauliques jouent un rôle crucial en déplaçant le fluide sous pression à travers tout le système. En cas de dysfonctionnement de ces pompes, c’est tout le processus qui est affecté, pouvant entraîner des arrêts de production et des coûts supplémentaires.
Des risques de pannes et de défaillances à ne pas négliger
Les centrales hydrauliques sont sujettes à divers types de pannes et de défaillances pouvant gravement impacter leur performance. Les pannes les plus courantes incluent les fuites de fluide, l’usure des composants, et les soucis de surchauffe.
Les principales causes des pannes
Les fuites de fluide hydraulique représentent une cause majeure de panne. Elles peuvent survenir en raison d’un joint usé, d’une fissure dans les tuyaux ou encore d’un mauvais raccordement. Chaque fuite implique une perte d’efficacité du système et un risque accru de contamination environnementale.
L’usure des composants est également une cause fréquente de défaillance. Les pièces mobiles comme les pompes et les vérins sont soumises à de fortes pressions et peuvent s’abîmer avec le temps. Sans une maintenance adéquate, ces éléments peuvent se détériorer rapidement.
La surchauffe de certains composants, telle que les moteurs ou les pompes, peut entraîner une diminution de la performance ou même un arrêt complet des opérations. Des systèmes de refroidissement inadéquats ou des conditions environnementales extrêmes peuvent être à l’origine de ces problèmes.
L’importance de la maintenance préventive
La meilleure façon de minimiser les risques de pannes et de défaillances est de mettre en place une maintenance préventive régulière. Cette approche proactive permet d’identifier les problèmes potentiels avant qu’ils ne deviennent critiques. Voici quelques stratégies clés pour une maintenance préventive efficace :
- Inspections régulières : Inspecter visuellement les composants critiques pour détecter d’éventuelles anomalies.
- Analyse de l’huile : Vérifier régulièrement la qualité et la pureté du fluide hydraulique pour éviter les contaminations.
- Remplacement des pièces usées : Changer systématiquement les pièces ayant atteint leur seuil de tolérance pour éviter les pannes soudaines.
- Maintenance prédictive : Utiliser des technologies avancées comme les capteurs et le suivi en temps réel pour prédire les pannes.
Les avantages clé de la maintenance préventive
- Une maintenance préventive bien planifiée offre de nombreux bénéfices. Elle réduit non seulement le risque de pannes coûteuses, mais aussi allonge la durée de vie des équipements. Les entreprises peuvent ainsi maintenir une productivité élevée et éviter des interruptions imprévues.
- Les coûts d’exploitation diminuent également. La prévention de pannes majeures permet de minimiser les interventions d’urgence, souvent bien plus onéreuses. Enfin, l’amélioration de l’efficacité énergétique et la réduction des déchets contribuent à une approche plus durable et respectueuse de l’environnement.
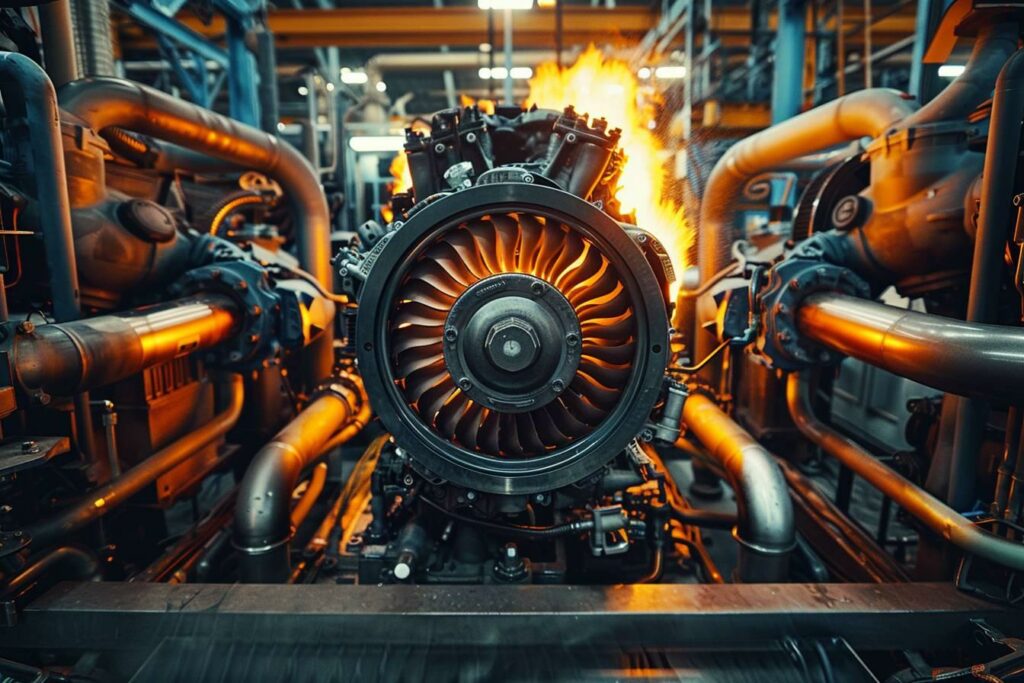
Le dépannage et la maintenance curative
Malgré une maintenance préventive rigoureuse, il arrive parfois que des pannes surviennent. C’est alors que la maintenance de centrales hydrauliques industrielles ou mobiles entre en jeu pour résoudre ces incidents de manière rapide et efficace. Voici les étapes cruciales dans la gestion d’une intervention de maintenance curative :
- Identification du problème : Diagnostiquer précisément l’origine de la panne.
- Réparation rapide : Intervenir rapidement pour limiter les impacts sur la production.
- Test et validation : Tester rigoureusement le système post-réparation pour assurer qu’il fonctionne correctement.
- Documentation : Documenter les interventions pour faciliter la maintenance future et les actions préventives.
Les avantages de la maintenance curative
La maintenance curative a pour principal avantage de permettre une reprise rapide des opérations. Lorsqu’une machine tombe en panne, il est fondamental de pouvoir la remettre en fonction aussi vite que possible pour éviter des pertes financières importantes. Outre la rapidité d’intervention, cette approche permet aussi de repérer les failles dans les processus de maintenance préventive. Chaque panne offre une opportunité d’apprentissage pour améliorer les protocoles futurs. Par exemple, une analyse des causes fondamentales peut révéler des points d’amélioration dans la routine de maintenance préventive.
Les nouvelles technologies au service de la maintenance des équipements et machines industrielles
Face à l’évolution rapide des technologies, le secteur de la maintenance hydraulique ne fait pas exception. Les innovations récentes offrent de nouvelles perspectives pour optimiser le fonctionnement des centrales hydrauliques.
Pour garantir la performance optimale des centrales hydrauliques industrielles, il est impératif d’allier maintenance préventive et curative. La surveillance régulière et les interventions rapides permettent de minimiser les arrêts de production et d’optimiser la durée de vie des équipements. Vous utilisez une centrale hydraulique et avez des besoins en maintenance préventive et curative ? N’hésitez pas à faire appel à un spécialiste, à l’instar de MPMD, expert du dépannage et entretien de centrales hydrauliques en Rhône-Alpes.
Commentaires récents